The LM9000 Continuous Laminating System’s modular design accommodates various numbers and types of materials. Each material is fed from adjustable spindles through guides and under a pressure capstan roller to assure complete adhesion to the plastic support backing. The system provides the ability to individually remove kiss cut adhesive liners for individual laminate materials.
For fragile materials like nitrocellulose, alignment is controlled through automated tracking. After lamination, the materials can either be cut and stacked in a collection chute or rewound onto a take-up reel. Other process steps such as dispensing, slitting, punching and inspection can also be integrated into the system.
For materials that are not available or cannot be processed in roll formats, a magazine feeding system for feeding the plastic support backing and more fragile materials is available. The system can also be enclosed for controlling the manufacturing environment.
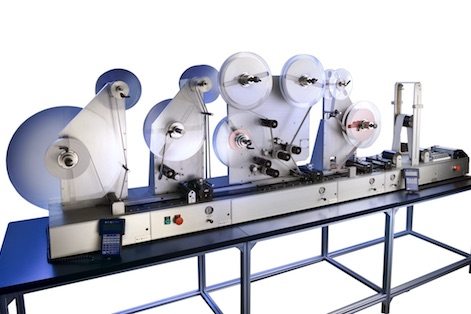
Product Features
Note: Material needs to be provided for Proof of Principle Study
Roll Feed
- Reel Feed
- Quick-Change Reel Payout Feed
Membrane Payout/3-up Payout/1-up and 2-up Cover Layer
- Reel Feed with Pivot Gate Capstan and Press Roller
- Quick-Change Reel Payout Feed
- Adjustable Material Guide
Cutter
- Press Roller
- Adjustable Material Guide
Take-up
- Quick Change Reel Take-up
Typical Applications
- Lateral Flow
- Immunoblots
- Dry Chemistry
- Custom applications
Product Specifications
Dimensions (L x W x H)
79 in x 20 in x 34 in (configuration dependent, excludes chassis)
Weight
approx 550 lbs (configuration dependent)
Power Requirement
110/220 VAC; 50/60 Hz
Air Requirement
Air Supply: 0–90 psi
Material Specifications
Plastic Backing
Width up to 120 mm
Reel Core 3.0 in (76 mm), 6.0 in (152 mm)
Reel OD 18.0 in (460 mm) max
Lamination Webs
Widths up to 100 mm
Reel Core: 3.0 in (75 mm)
Reel OD: 12 in. or 16 in. max
Membrane Width
Minimum: 0.20 in (5 mm)/Material dependent
Maximum: 4.64 in (118 mm)